先进陶瓷作为重要的结构/功能一体化材料,其独特的性能具有不可替代性,在航天航空、新能源汽车、半导体、高端装备等新兴战略产业和国防工业具有巨大的应用前景,具有不可或缺的作用,重点产品应用发展迅速。未来,先进陶瓷材料在哪些行业中发展值得关注呢?
据中国汽车工业协会最新数据,1至11月,我国新能源汽车产销分别完成625.3万辆和606.7万辆,同比均增长约1倍,市场占有率达25%。除了产销增长幅度远超市场同期,新能源车的渗透率也已经超过36%,且依然在不断提升。随着电动汽车技术的不断进步,其零部件材料及设计更替加速,先进陶瓷材料凭借其特殊的性能优势在新能源电动汽车的应用中体现的淋漓尽致。
其中,HIP氮化硅轴承球和高导热氮化硅基板极为热门。
新能源汽车的电机轴承相比传统轴承转速高,需要密度更低、相对更耐磨的材料,氮化硅陶瓷轴承中的球在轴承组件内产生更少的摩擦、更少的热量,尤其是氮化硅是天然的电绝缘体,可减少轴承放电产生的电腐蚀,避免出现缩短轴承和润滑剂的使用寿命,最终导致轴承失效的现象发生,非常适合应用于电动汽车等领域。
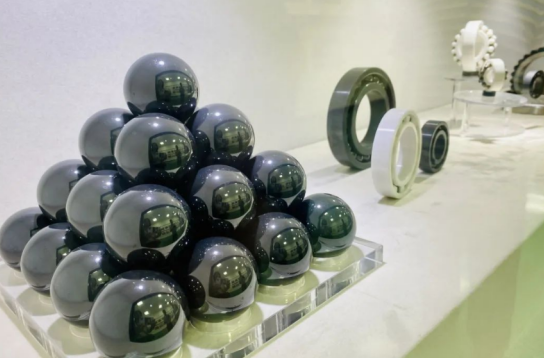
在电驱时代下,陶瓷轴承取代钢球轴承已是一种趋势,如特斯拉采用的电机中输出轴是用陶瓷轴承,采用NSK设计的混合陶瓷轴承,轴承滚珠采用50个氮化硅球组成;国内小鹏P7、G9、蔚来ET7等车型均采用氮化硅陶瓷球绝缘轴承。在制备方面,目前应用最广泛的氮化硅陶瓷球烧结工艺为热等静压烧结(HIP)和气压烧结(GPS),两种工艺下生产的陶瓷球针对不同的使用环境都有广泛的应用。与GPS氮化硅相比,HIP氮化硅具有更好的力学性能,更高的疲劳寿命。
目前高端陶瓷轴承产品生产仍以日本、欧美企业为主导,国际市场占有率、发展方向的引领力仍然被国外知名企业所控制。而我国在2015年中材高新氮化物陶瓷有限公司突破了热等静压氮化硅陶瓷球批量化制造技术,成为继美国库斯泰克、日本东芝之后第三家,也是国内首家形成批量化生产热等静压氮化硅陶瓷材料的企业,产品出口到瑞典斯凯孚、美国铁姆肯、德国GMN、西班牙福赛等地。另外,国瓷金盛等采用相似的工艺能够制备出弯曲强度达到1000 MPa的氮化硅轴承球。
氮化硅陶瓷基板主要应用于纯电动汽车(EV)与混合动力汽车(HEV)的动力装置、半导体器件和逆变器等市场领域,具有巨大的市场潜力与应用前景。
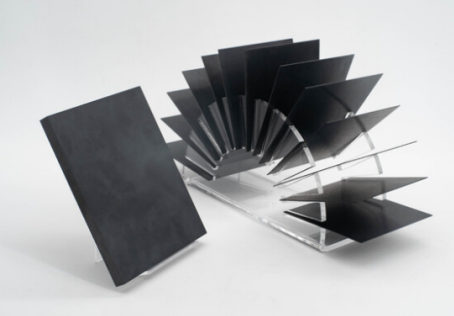
现阶段,商业应用的高热导氮化硅陶瓷基板材料要求热导率≥85 W/(m·K),弯曲强度≥650MPa,断裂韧性5~7MPa·m1/2,而真正具备大规模生产高导热氮化硅陶瓷基板能力的企业主要有东芝集团、日立金属株式社、日本电气化学、日本丸和与日本精细陶瓷。国内对氮化硅陶瓷基板材料的研究也取得部分进展。中材高新氮化物陶瓷有限公司北京分公司以流延成型工艺制备的氮化硅陶瓷基板热导率为100 W/(m·K);北京中材人工晶体研究院有限公司通过优化烧结方式与工艺,成功制备出弯曲强度700-800MPa,断裂韧性≥8MPa·m1/2,热导率≥80W/(m·K)氮化硅陶瓷基板。目前,随着新能源汽车渗透率不断提高,加之AI技术的出现,也使得的电动汽车逐步向智能化发展,不少陶瓷材料也被汽车制造商关注,如高容MLCC、碳陶刹车、激光雷达封装材料、陶瓷导热材料等。
半导体行业遵循“一代技术、一代工艺、一代设备”的产业规律,而半导体设备的升级迭代很大程度上依赖于精密零部件的技术突破。其中,精密陶瓷部件是最具有代表的半导体精密部件材料,其在化学气相沉积、物理气相沉积、离子注入、刻蚀等一系列半导体主要制造环节均有重要应用。如轴承、导轨、内衬、静电吸盘、机械搬运臂等。尤其是在设备腔体内部 ,发挥支撑、保护、导流等功能。
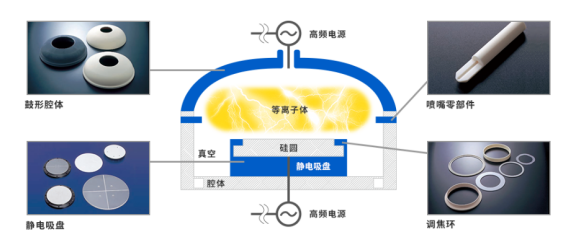
2023年以来,荷兰、日本也先后发布对管制新规或外贸法令,对光刻机在内的半导体设备增加出口许可令规定,半导体逆全球化趋势逐渐显露,供应链自主可控重要性日益突出。面对半导体设备零部件国产化的需求,国内企业正积极推动产业发展。中瓷电子实现了加热盘和静电卡盘等技术难度高的精密零部件国产化,解决国产半导体设备行业“卡脖子”问题;国内头部SiC涂层石墨基座、SiC蚀刻环供应商德智新材在顺利完成亿元融资等.....
国家“双碳”政策的引导下,各行各业逐步向节能、降碳、减污、增效等方向发展。陶瓷行业在此背景下,面临能耗与环保压力,但同时也给陶瓷材料带到新的发展机遇。
以陶瓷膜为核心的膜分离技术目前主要作为高效分离工艺在过程工业以及特种水处理领域中的过滤分离、浓缩提纯、净化除杂等工艺环节用于替代传统过滤分离技术。
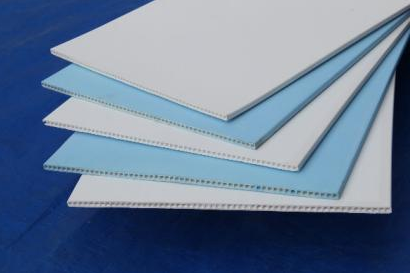
其中,高性能的陶瓷平板膜能够实现复杂环境下流体的过滤、分离及提纯,具有耐高温高压、化学稳定性好、过滤效率高、可靠性好、运行维护成本低、使用寿命长、全生命周期绿色化等特点。已在工业园区废水治理、中水回用、黑臭水体治理、市政污水及分布式水处理等领域实现了规模化推广及应用,具有广阔的市场前景,是当前国际高性能陶瓷分离膜领域最主要的发展方向。除了水处理,我国大气污染治理也迫在眉睫。脱硝除尘高温纤维膜是以陶瓷纤维复合膜材料为支撑体,通过负载环境友好型稀土--金属氧化物体系的纳米脱硝催化剂而制备的具有除尘脱硝一体化功能的过滤元件,能够实现高温状态下气体的直接净化。
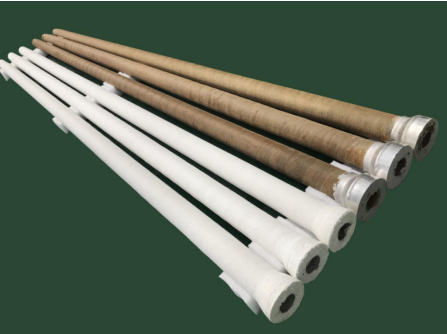
气凝胶作为超级绝热材料,全面绿色低碳发展为气凝胶产业发展带来了前所未有的机遇。在加快推动绿色产业发展的趋势下,气凝胶新技术有望与绿色制造发展相结合,形成更多新产品应用。
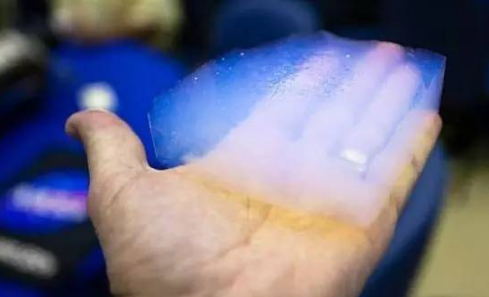
气凝胶具有极低密度、超高孔隙率、低折射率、低热导率、低声阻抗等特性,这是一般固态材料所不具备的。这些特性使其在隔热保温、生物医学、隔音、吸附等领域具有巨大的应用前景,市场需求潜力巨大。
随着社会的发展和人们生活的改善,人工植入物和人工器官的临床应用将越来越广泛。不锈钢、钴合金等金属材料因具有优异的机械性能和控制性能,在我国长期被作为骨科固化和修复材料,但金属材料生物相容性较差。因此,相容性更好和更健康的生物陶瓷或涂层材料的研究和市场都处于爆发增长中。生物医用陶瓷中如Al2O3、ZrO2、ZTA、Si3N4以及它们的复合陶瓷材料等,由于断裂韧性、耐磨性优良,常应用于外科手术承重假体、牙科移植物、骨头替代物等。其中,氮化硅的杀菌作用和自润滑特性相结合,其做种植体,具有长期稳定的生物稳定性;氧化锆因性能良好且美观,但强度由于玻璃陶瓷,常用于牙科修复材料。
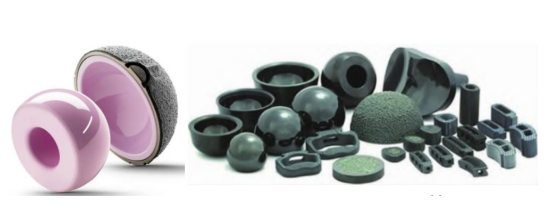
2022年全球医用陶瓷材料市场规模约为150亿美元。在中国,2022年医用陶瓷材料市场规模约为45亿美元。其中氧化铝陶瓷占比最大,约60%。氧化锆陶瓷用于牙科领域较多,氮化硅陶瓷用于骨科植入物。
在各种极端应用环境下,陶瓷总是能凭借其优异的性能脱颖而出,其中,航空航天和军工都是先进陶瓷非常火爆的应用市场。而在航空航天市场中,“耐高温”和“隐身”就是陶瓷的两条发展主线。随着单晶、热障涂层及主动气冷的潜力逐渐穷尽,新一代军用航空发动机对新型耐高温结构材料的需求愈发迫切,SiC/SiC-CMC成为耐高温结构材料首选之一。碳化硅纤维在SiC/SiC-CMC中起到主要的增强增韧作用,耐温能力1200℃以上的碳化硅纤维作为SiC/SiC-CMC最关键的原材料,成为各航空强国的研究竞争重点。
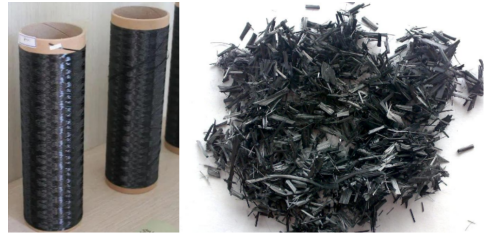
吸波材料是最重要的隐身材料之一,一般由基体材料(或粘结剂)与吸收介质(吸收剂)复合而成。在陶瓷吸波材料中,碳化硅是制作多波段吸波材料的主要成分;陶瓷红外隐身材料是一种由无机陶瓷纳米材料与无机高分子材料复合而成的涂料,通过精细控制无机陶瓷纳米粒子均匀分散在无机聚合物基体中,实现高效的宽频带电磁波吸波。
|